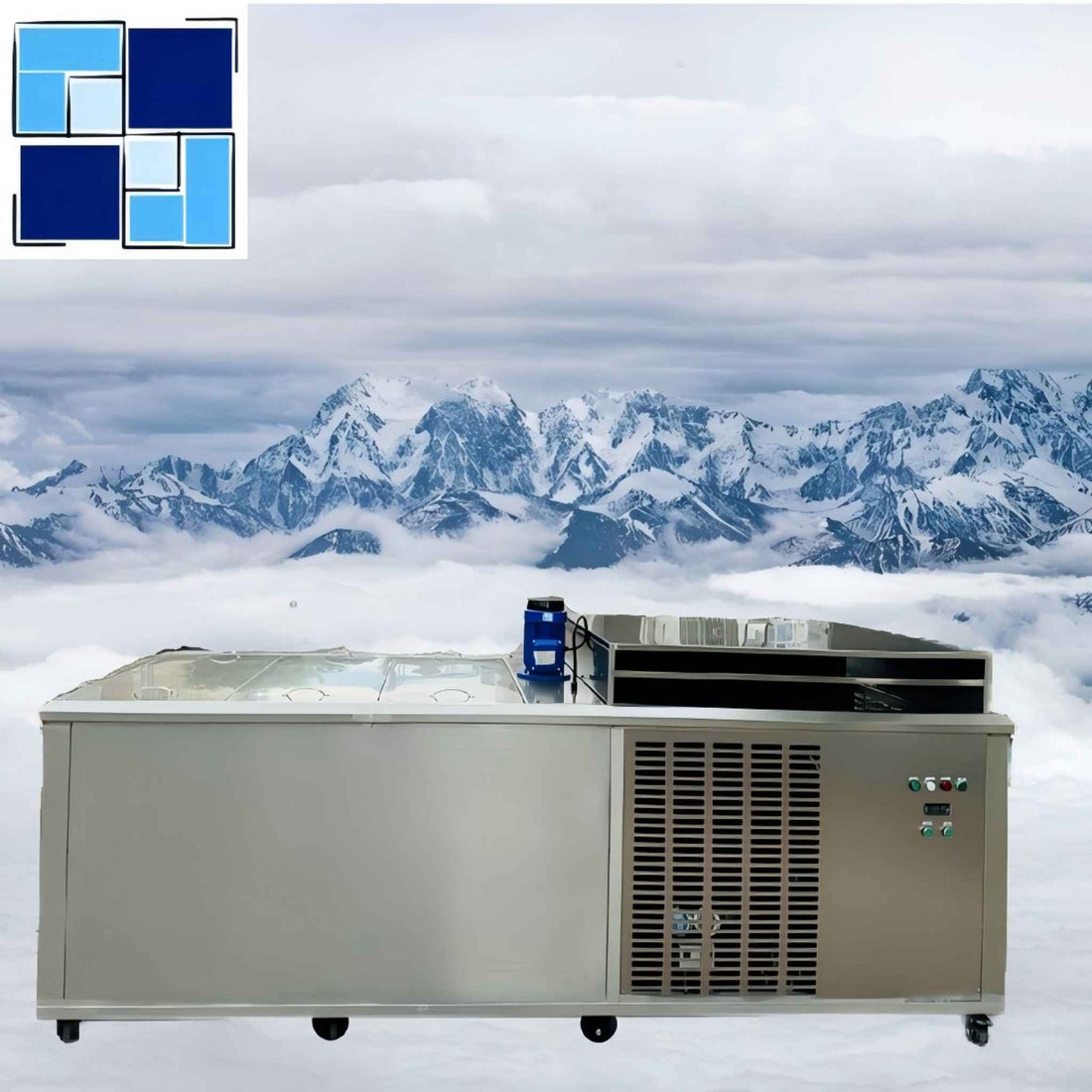
The Impact of Ethylene Glycol, Propylene Glycol, and Saltwater on Brine Block Ice Machines
Compartir
Brine block ice machines rely on cooling media to transform water into dense, solid ice blocks (typically 10–50kg), widely used in fisheries, food logistics, and industrial cooling. The choice of cooling medium—ethylene glycol, propylene glycol, or saltwater—directly affects ice quality, equipment lifespan, and operational costs. Understanding their unique properties helps optimize machine performance and align with specific application needs. Here’s a detailed breakdown of their impacts:
1. Ethylene Glycol: The Low-Temperature Powerhouse with Toxicity Considerations
Ethylene glycol is prized for its extremely low freezing point (down to -40°C when fully concentrated), making it ideal for high-capacity machines operating in subzero environments, such as Arctic fisheries or industrial freezers. Its high thermal conductivity (0.25 W/m·K at 20°C) ensures rapid heat transfer, reducing ice-making cycles by 15% compared to saltwater. However, its toxicity (LD50: 8540 mg/kg in rats) poses risks in food-contact scenarios—even trace leaks can contaminate ice used for seafood preservation, leading to regulatory penalties.
Material compatibility is another challenge: ethylene glycol mixed with water creates a mildly acidic solution that accelerates corrosion in unprotected steel components. Machines using ethylene glycol require annual inspections of rubber seals and copper coils, increasing maintenance costs by 20%. Despite these drawbacks, it remains the go-to choice for non-food industrial applications demanding ultralow temperatures and fast ice production.
2. Propylene Glycol: The Food-Safe Alternative with Balanced Performance
Propylene glycol emerges as the preferred option for food-grade environments, thanks to its non-toxic nature (GRAS-listed by the FDA for indirect food contact) and moderate freezing point (-25°C at 50% concentration). Its viscosity (60 mPa·s at 20°C) is 30% higher than ethylene glycol, slightly reducing heat transfer efficiency—ice-making cycles may extend by 5–10%—but its safety benefits outweigh this trade-off in applications like meat processing or pharmaceutical logistics, where ice directly contacts consumables.
Propylene glycol’s neutral pH (7.0–9.0 when diluted) minimizes corrosion, cutting down on anti-corrosive additives and reducing annual maintenance by 30%. For example, a seafood processing plant using propylene glycol in its brine system reported a 40% longer lifespan for evaporator coils compared to its previous saltwater setup. While it costs 25% more than ethylene glycol per liter, the reduced contamination risks and lower repair costs make it a cost-effective long-term choice for food-related industries.
3. Saltwater (Sodium Chloride Solution): The Economical Option with Corrosion Challenges
Saltwater is the most budget-friendly cooling medium, with a freezing point of -18°C at 23% concentration—sufficient for standard ice-block production in tropical fisheries or beverage logistics. Its low cost (5–10% of glycol prices) and ease of preparation attract small-scale operators. However, its aggressive corrosiveness is a major drawback: chloride ions in saltwater cause pitting corrosion on metal surfaces, especially aluminum and uncoated steel, leading to leaks in as little as 1–2 years without proper treatment.
To mitigate corrosion, users must add inhibitors (e.g., potassium dichromate) and perform monthly system flushes, increasing operational complexity. A case study in a Southeast Asian fish market found that saltwater-based machines required twice as many coil replacements as glycol-based models over a five-year period, eroding the initial cost savings. Despite these issues, saltwater remains popular in short-term or low-investment setups where strict food safety isn’t a priority and rapid ice production at minimal cost is the primary goal.
Key Considerations for Choosing a Cooling Medium
Application Safety: Prioritize propylene glycol for food contact (e.g., seafood, pharmaceuticals) to comply with hygiene standards.
Temperature Requirements: Use ethylene glycol for extreme cold (-30°C or lower); saltwater suffices for moderate climates (above -15°C).
Maintenance Budget: Factor in corrosion prevention costs—saltwater systems need frequent upkeep, while propylene glycol systems offer lower long-term maintenance.
QIANRUI Brine Block Ice Machines: Engineered for Medium-Specific Performance
QIANRUI designs its machines to optimize each cooling medium’s strengths while mitigating risks:
Material Resistance: All models feature 316L stainless steel evaporators and PTFE-coated pipelines, reducing corrosion by 60% in saltwater environments and eliminating material compatibility issues with glycols.
Smart Monitoring: Built-in pH sensors and conductivity meters alert users to medium degradation, preventing ice quality fluctuations and equipment damage.
Energy Efficiency: Patented spiral heat exchangers maximize thermal transfer, offsetting the viscosity-related efficiency loss in propylene glycol systems to ensure consistent ice production rates.
Whether your needs demand food-grade safety, extreme cold tolerance, or budget efficiency, QIANRUI’s customizable solutions ensure your brine block ice machine operates at peak performance. Choose the cooling medium that fits your application, and let our technology handle the rest.
Ethylene glycol, propylene glycol, and saltwater each bring unique advantages and challenges to brine block ice machines. The right choice depends on your industry’s safety requirements, operational temperature, and maintenance capacity. By understanding these impacts, you can select a cooling medium that balances performance, cost, and longevity. QIANRUI’s engineering expertise ensures seamless integration with any medium, delivering reliable ice production across fisheries, food logistics, and industrial cooling—because optimal ice quality starts with the right cooling foundation.